CAD system embedded in ESPRIT CAM
Simple and convenient 3D editor that expands the basic functionality of ESPRIT CAM
LO CNITI is a developer and supplier of software for production. The company specializes in implementing CAD and CAM systems, developing post-processors for CNC machines, and providing user training.
Problem
ESPRIT is a CAM system for CNC programming, optimization, and simulation. It helps control the production of parts with complex geometries on all types of metal-cutting equipment. The system is one of the ten most popular CAM systems in the world and has been used for many years in the factories of companies such as Audi, Boeing, and Siemens.
ESPRIT’s weak point was the lack of tools for working with model geometry. When the model needed adjustments, production engineers could not make the changes themselves and had to return the 3D model to the designers in CAD. This complicated the interaction between departments and delayed the production process.
LO CNITI, as the official distributor, needed to create a CAD subsystem for 3D solid modeling within ESPRIT CAM.
Solution
Our analysts surveyed Russian ESPRIT users and collected requirements for the future CAD system. In addition to tools for editing 3D models in production, users required support for dimensional and logical constraints and the ability to import major exchange formats (STEP, STL, etc.).
To meet these requirements, a reliable geometric kernel was necessary. Considering the project’s needs for speed and cost-effectiveness, we chose the C3D kernel from the C3D Labs company. The well-known CAD system KOMPAS-3D is also based on C3D.
Rubius is a C3D Labs authorized developer. We contributed to various CAD software development, based on C3D, as well as the geometry kernel itself.
The C3D geometric modeling kernel combines five crucial CAD modules. It includes a C3D Modeler that performs all geometric calculations necessary for constructing 2D sketches and 3D models; a C3D Solver that adds dimensional control and constraints; a C3D Vision that visualizes 3D models with ease; a C3D converter that imports and exports geometric models and their attributes; and a C3D B-shaper that converts polygonal meshes to b-rep solids.
We developed the ESPRIT Extra CAD, a CAD software, based on C3D, and embedded it in ESPRIT CAM. It allows users to refine 3D models directly within ESPRIT.
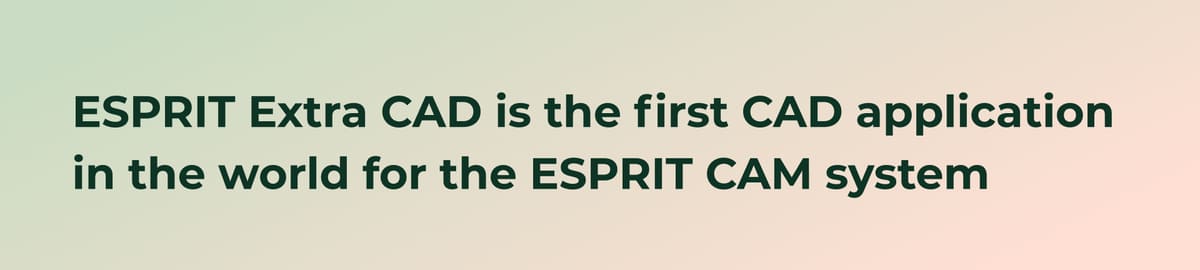
ESPRIT Extra CAD capabilities include:
- model tree management
- model editing within CAM (chamfering, extruding, rotation)
- 2D limits adaptation for drafts in 3D using a geometric solver
- support for 3D constraints for creating assembly units
- wide format support for input and output data (STEP, SPL, Parasolid, ACIS, IGES, STL, VRML)
Results
The development of the first version of ESPRIT Extra CAD took six months. The result is a simple and convenient 3D editor that expands the basic functionality of ESPRIT CAM. Users of the system can adapt models to the specifics of production on CNC machines without wasting time transferring data between CAD/CAM and departments. This, in turn, helped speed up production and improve the quality of the finished products.
ESPRIT Extra CAD was presented to the world at the ESPRIT World Conference in San Diego, USA.
We received a lot of positive feedback from users, as well as interest in development from the ESPRIT vendor. Extra CAD was built directly into the CAM system interface, enabling users to work with CAD files without installing additional software.
Subsequently, Rubius updated the functionality of ESPRIT Extra CAD as new versions of the C3D kernel were released.
Customer's feedback
Rubius is a team with a high level of project management. The entire interaction process was seamless, and we always knew at what stage the development was, and solved all issues together.
Let’s discuss your project
Tell us about your requirements and we’ll get back with a possible technical solution